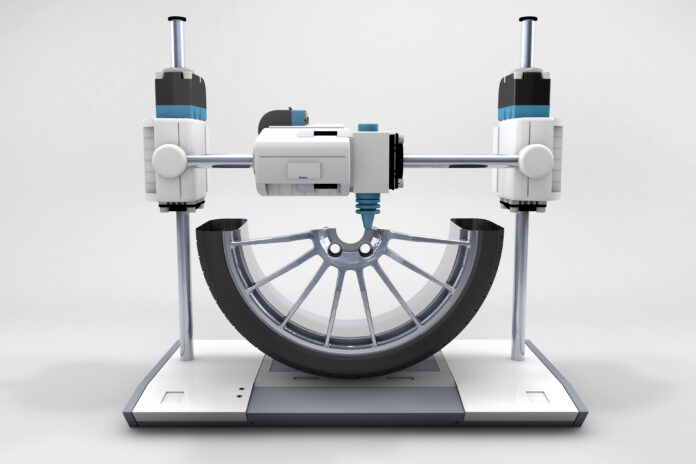
The automotive industry faces multifaceted demands, ranging from the necessity for innovative, high-performing vehicles to the optimization of production processes and supply chain logistics. Addressing these challenges is the burgeoning technology of 3D printing.
Increasingly, 3D printing finds application across all facets of automotive production. Beyond its traditional role in rapid prototyping, this technology is now utilized for manufacturing tooling and, in some instances, final parts.
As the scope of automotive 3D printing applications continues to broaden, below are some notable examples of automotive companies leveraging this technology to bolster their production capabilities.
1. BMW’s Lightweighting Initiative
BMW utilizes 3D printing to advance its lightweighting efforts, a crucial aspect of automotive design aimed at enhancing fuel efficiency and performance. By leveraging selective laser melting (SLM) technology, BMW produces intricate structural components, such as chassis brackets and suspension parts, with optimized geometries that reduce weight without compromising strength. This approach allows BMW to achieve significant weight savings compared to traditional manufacturing methods, contributing to improved vehicle dynamics and fuel economy. Additionally, 3D printing enables BMW to streamline the production process, reduce material waste, and accelerate design iterations, ultimately enhancing the competitiveness of its vehicles in the market. Through its innovative lightweighting initiative, BMW demonstrates the transformative potential of 3D printing in shaping the future of automotive engineering and manufacturing.
2. Volkswagen Autoeuropa: 3D-printed Manufacturing Tools
Volkswagen Autoeuropa exemplifies the shift towards 3D printing for tooling within the automotive sector. By leveraging Ultimaker’s 3D printers, Volkswagen has substantially reduced tool production costs and lead times. This transition not only enhances efficiency but also promotes ergonomic improvements and operational cost savings.
3. Ford’s Application of 3D Printing in High-Performance Vehicles
Ford Motor Company harnesses 3D printing to push the boundaries of vehicle design. In the development of its 2020 Shelby GT500, virtual testing and rapid prototyping with 3D-printed components were instrumental. Ford’s integration of 3D printing into its manufacturing process underscores its commitment to innovation and performance.
4. Porsche’s 3D-printed Custom Seats
Porsche has introduced a groundbreaking concept for sports car seating, incorporating 3D printing and lattice design. These seats feature polyurethane 3D-printed central sections, allowing for customizable firmness levels. By embracing personalized seating reminiscent of motorsport standards, Porsche pioneers advanced comfort and performance for its customers.
5. Innovative Security Solutions: 3D-printed Lug Nuts
Ford pioneers 3D-printed locking wheel lug nuts to combat theft. By creating customized, unique patterns that defy replication, Ford enhances vehicle security. This innovative approach highlights the adaptability and security benefits of 3D printing in automotive applications.
6. Driving Innovation in Motorsports with 3D Printing
In motorsports, 3D printing emerges as a key enabler of performance optimization. Through wind tunnel testing and rapid prototyping, teams like Alfa Romeo Sauber F1 and Volkswagen Motorsport achieve unparalleled design flexibility and efficiency. The integration of 3D-printed components into racing vehicles exemplifies the technology’s role in pushing the boundaries of automotive engineering.
7. 3D Printing for Automotive Brackets
Traditionally mundane, brackets now undergo optimization with 3D printing. Rolls Royce showcases this with a batch of 3D-printed metal parts, boasting innovative features such as embedded branding and unique identification. This approach not only enhances design flexibility but also streamlines production and reduces costs.
8. Enhanced Customization with 3D Printing
Automakers like Daihatsu and Volkswagen capitalize on 3D printing to offer personalized vehicle components. By partnering with Stratasys and HP, these companies enable customers to customize parts, enhancing both functionality and aesthetic appeal. This shift towards customization underscores 3D printing’s potential to transform automotive design and production.
9. 3D Printing Spare Parts for Classic Cars
Porsche Classic pioneers the use of 3D printing to produce rare spare parts for vintage models. By leveraging additive manufacturing, Porsche addresses the challenges of obsolete tooling and low-volume production. This approach not only preserves automotive heritage but also demonstrates the economic viability of 3D printing for aftermarket applications.
10. Local Motors & XEV: Pioneering 3D-printed Cars
Companies like Local Motors and XEV lead the charge towards fully 3D-printed vehicles. Leveraging large-format 3D printers, these companies aim to revolutionize car production. By embracing distributed manufacturing models and rapid prototyping, they redefine the automotive industry’s approach to design and production.
11. The Future of Motorcycle Production: 3D Printing
The motorcycle industry explores the potential of 3D printing to revolutionize production. Projects like APWORKS’ Light Rider and BigRep’s NERA motorcycle offer glimpses into this future. With lightweight components and rapid production capabilities, 3D printing holds promise for enhancing motorcycle design and performance.
As these examples illustrate, 3D printing is driving the future of automotive production. From personalized seating to innovative security solutions, this technology offers unprecedented opportunities for customization, efficiency, and performance optimization. As automakers continue to embrace 3D printing across the value chain, the automotive industry stands poised for a new era of innovation and transformation.