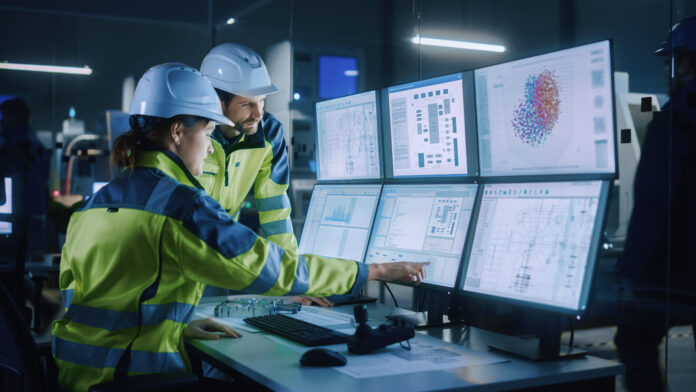
In the competitive world of manufacturing, ensuring high-quality products is paramount. The integration of Artificial Intelligence (AI) with Manufacturing Execution Systems (MES) is revolutionizing quality control, enabling real-time monitoring, and enhancing production processes. This article explores the benefits, applications, and best practices of using AI in MES for real-time quality control.
Understanding AI in MES
What is a Manufacturing Execution System (MES)?
A Manufacturing Execution System (MES) is a software platform that manages and monitors production operations on the factory floor. It collects real-time data on production processes, enabling manufacturers to control, track, and optimize their operations.
Role of AI in MES
AI in MES involves using artificial intelligence algorithms to analyze production data, identify patterns, and make real-time decisions. By integrating AI, MES can enhance predictive maintenance, quality control, and overall production efficiency.
For an in-depth overview of MES, refer to ISA’s MES Guide.
Benefits of Integrating AI with MES
Enhanced Quality Control
AI algorithms can analyze data from various production stages to detect defects and anomalies in real time. This proactive approach ensures that quality issues are identified and addressed promptly, reducing waste and improving product quality.
- Example: An automotive manufacturer uses AI in MES to monitor welding processes, detecting inconsistencies and preventing defects before they propagate.
Predictive Maintenance
AI can predict equipment failures by analyzing data from sensors and historical maintenance records. This allows for scheduled maintenance before a breakdown occurs, minimizing downtime and extending equipment lifespan.
- Example: A semiconductor plant leverages AI-driven MES to predict and prevent equipment failures, maintaining high uptime and production quality.
Process Optimization
AI in MES can continuously analyze production data to identify inefficiencies and recommend improvements. This leads to optimized processes, reduced cycle times, and increased throughput.
- Example: A pharmaceutical company uses AI to optimize batch production processes, enhancing yield and consistency.
For further insights into AI’s role in manufacturing, explore McKinsey’s Report on AI in Manufacturing.
Applications of AI in MES
Real-Time Defect Detection
AI-powered MES can use computer vision and machine learning algorithms to inspect products for defects in real time. This technology can analyze images and sensor data to detect defects that may be missed by human inspectors.
- Tool: TensorFlow and OpenCV are popular frameworks for developing AI-based defect detection systems.
Adaptive Process Control
AI enables MES to adjust process parameters dynamically based on real-time data. This adaptive control ensures that production processes remain within optimal ranges, enhancing product quality and consistency.
- Tool: Python and R are commonly used for developing adaptive process control algorithms.
Supply Chain Optimization
AI in MES can also improve supply chain efficiency by predicting demand, optimizing inventory levels, and managing logistics. This ensures that materials and products are available when needed, reducing delays and costs.
- Tool: Supply chain optimization platforms like Llamasoft and Kinaxis incorporate AI for enhanced decision-making.
For more information on AI applications in MES, visit Deloitte’s AI in Manufacturing Page.
Best Practices for Implementing AI in MES
Data Integration
Ensure seamless integration of AI with MES by consolidating data from various sources such as sensors, machines, and enterprise systems. A robust data infrastructure is essential for accurate analysis and decision-making.
- Practice: Use data lakes or data warehouses to centralize and manage production data.
- Benefit: Improved data accessibility and reliability for AI algorithms.
Selecting the Right AI Tools
Choose AI tools and frameworks that are compatible with your MES and tailored to your specific industry needs. Open-source tools like TensorFlow, PyTorch, and commercial platforms like IBM Watson can be considered based on your requirements.
- Practice: Evaluate AI tools based on scalability, ease of integration, and support.
- Benefit: Ensures efficient deployment and scalability of AI solutions.
Continuous Monitoring and Improvement
Implement a continuous monitoring system to track the performance of AI algorithms and make necessary adjustments. Regularly update models with new data to maintain accuracy and relevance.
- Practice: Set up dashboards and alerts to monitor key performance indicators (KPIs).
- Benefit: Ensures ongoing improvement and adaptation to changing production conditions.
For guidelines on best practices, refer to Gartner’s Guide on AI in Manufacturing.
Challenges and Future Trends
Data Quality and Quantity
Ensuring high-quality and sufficient data for training AI models is a significant challenge. Manufacturers must invest in data collection and preprocessing to achieve accurate and reliable AI outcomes.
Integration Complexity
Integrating AI with existing MES can be complex and require significant changes to infrastructure. Collaboration between IT and production teams is crucial for successful implementation.
Future Trends
- Edge AI: Deploying AI at the edge, close to production equipment, to reduce latency and enhance real-time decision-making.
- Explainable AI: Developing AI systems that provide transparent and understandable decision-making processes to build trust and compliance.
For more on future trends, explore Forrester’s AI Predictions.
Master AI in MES to Improve Operational Efficiency
Integrating AI with Manufacturing Execution Systems (MES) offers transformative benefits for real-time quality control, predictive maintenance, and process optimization. By leveraging AI, manufacturers can enhance product quality, reduce downtime, and optimize operations. Implementing best practices such as data integration, selecting the right AI tools, and continuous monitoring is crucial for success. As AI technology evolves, staying abreast of emerging trends will further enhance the capabilities and efficiency of MES in the manufacturing industry.