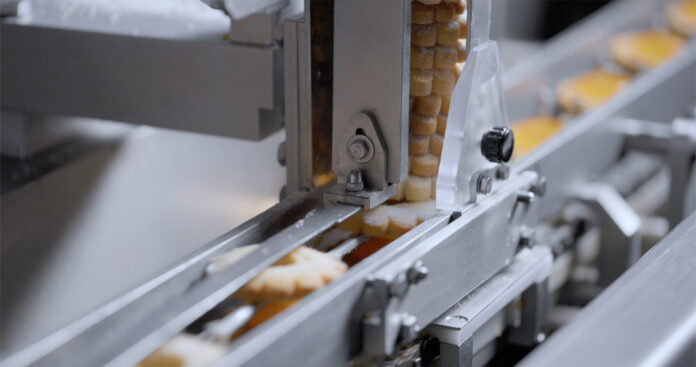
Ransomware crews have learned that an hour of downtime on a pasteurization, bottling, or packaging line can cost six figures. In 2024 alone, a dozen publicly disclosed cyber‑incidents struck global food companies, from dairy processors in New Zealand to U.S. coffee distributors, causing shipment delays and product recalls. The U.S. government even issued a joint CISA/FBI alert on ransomware threats to the Food & Ag sector.
Food plants are tempting targets because most still run 1990‑era PLCs on flat networks and seldom patch firmware. Once attackers land on the IT side (via phishing or a vulnerable VPN), they can pivot into production with minimal resistance.
Zero Trust in Plain English
Zero Trust flips the old “moat‑and‑castle” model on its head: no user, device, or packet is trusted by default—ever. Every request must prove it belongs, and every asset gets only the access it truly needs.
Industrial vendors now publish OT‑specific frameworks that translate Zero Trust into plant‑floor reality, including:
- Rockwell Automation’s Zero‑Trust Architecture
- Dragos’ guide to implementing Zero Trust in OT environments
- TXOne’s OT Zero‑Trust Handbook
All three converge on three pillars:
- Strong Identity & Authentication – Certificates or hardware roots of trust for every PLC, HMI, and historian.
- Least‑Privilege Micro‑Segmentation – Break the “flat” network into micro‑zones so a breach in packaging can’t reach pasteurization.
- Continuous Monitoring & Response – Passive sensors watch for rogue traffic or policy violations 24/7.
Unique Constraints in Food & Beverage Facilities
Constraint | Why It Matters | Practical Work‑Around |
---|---|---|
24 × 7 production cycles | Taking a line down for patching jeopardizes perishable inventory. | Use inline “virtual patching” via industrial firewalls to block exploits until a maintenance window. |
Legacy controllers with no encryption | Many SLC 500 and early ControlLogix PLCs can’t run agents or TLS. | Place them in locked‑down micro‑segments; proxy all traffic through an inspection gateway. |
Strict hygiene & safety rules (FSMA, USDA) | Physical access to cabinets is limited; downtime triggers regulatory audits. | Employ cabinet‑door‑closed firmware updates and remote monitoring. |
Seasonal contract workforces | High badge turnover increases insider risk. | Enforce MFA for every remote login and time‑bound access tokens for vendors. |
Five‑Step Roadmap to Zero Trust on the Plant Floor
- Map & Prioritize Assets
Run a passive scan for 30 days to build a live inventory; tag each line with its revenue impact. - Carve Micro‑Zones
Start with a DMZ between IT and OT, then segment process cells (e.g., pasteurizer, filler, labeler) into their own VLANs with Layer‑3 firewalls. - Deploy Identity‑Aware Gateways
Swap out flat VPN tunnels for gateways that verify certificates, user roles, and device health before any command hits the PLC. - Apply Inline Virtual Patching
Industrial IPS filters block known exploits against un‑patchable firmware while you schedule real maintenance. - Monitor, Measure, Iterate
Track three KPIs: (a) policy violations blocked, (b) MTTD (Mean Time To Detect) < 5 min, (c) unplanned OT downtime hours per quarter.
Regulatory & Insurance Tailwinds
- ISA/IEC 62443 certification is becoming a bid requirement for co‑packers and private‑label suppliers.
- Insurers increasingly demand segmentation and MFA as conditions for cyber‑policy renewal; plants that document Zero Trust controls see premiums fall 10–15 %.
- FSMA requires “preventive controls” for food safety—cyber‑induced spoilage or mis‑labeling now counts.
What Success Looks Like
Metric | Target | Why It Pays Off |
---|---|---|
Unplanned OT downtime | ↓ 50 % YoY | Less scrap and fewer retailer charge‑backs |
Ransomware dwell time | Contained to IT; 0 minutes in OT | Attackers can’t reach PLCs, so production continues |
Patch lag on critical CVEs | Virtually patched in < 24 h | Shrinks the attacker window dramatically |
Dragos reports that food manufacturers adopting Zero Trust and segmentation cut ransomware‑related downtime costs by 30–40 % within 12 months.
Common Pitfalls (and Easy Fixes
Pitfall | Quick Fix |
---|---|
Wi‑Fi engineers lack 3GPP/ICS skills | Cross‑train or use a managed OT‑SOC for Year 1. |
Undefined slice or zone KPIs | Draft SLA‑grade specs—latency, jitter, bandwidth—before rollout. |
Regulatory surprise on radio or cabinet access | Loop in QA and safety teams during design, not after deployment. |
Shadow IT adding rogue HMIs | Enforce device attestation; block anything without a signed cert. |
Executive Cheat‑Sheet
- Which production line loses us the most dollars per minute of downtime?
- How quickly can we inventory every PLC, HMI, and sensor?
- Who owns enforcement when a policy violation fires at 2 a.m.—IT, OT, or both?
- What is the Cost of Inaction if ransomware halts packaging for 48 hours?
Key Takeaways
- Food & Beverage OT is now a top ransomware target; the federal government is sounding the alarm.
- Zero Trust translates to three concrete controls: authenticated devices, micro‑segmentation, and continuous monitoring.
- Start with passive asset discovery, pilot in one high‑value line, and let success fund expansion.
- Within two budget cycles, fewer recalls, lower downtime, and reduced insurance premiums should more than cover the investment.
The bottom line: Zero Trust isn’t a buzzword—it’s a practical, revenue‑protecting upgrade that keeps the conveyor belts turning and the auditors smiling. With turnkey toolkits from leaders like Rockwell Automation, Dragos, and TXOne Networks, even plants running legacy controllers can adopt Zero Trust—without locking operators out or shutting lines down.