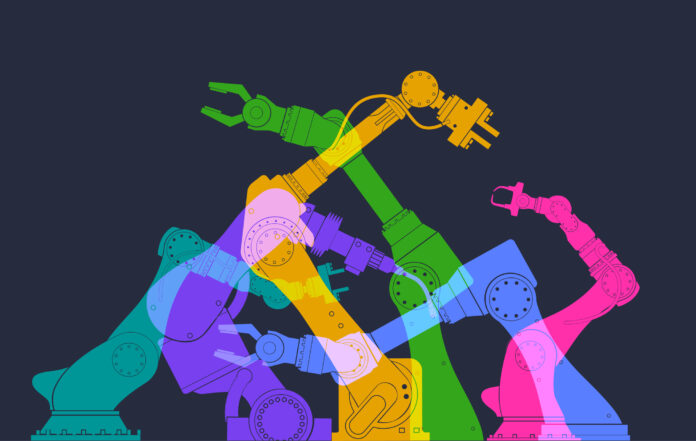
Collaborative robots, or cobots, represent a specialized category of industrial robots explicitly designed to work alongside human operators in shared workspaces. They’re unlike the conventional industrial robots that typically function in isolated environments behind safety barriers. Cobots are equipped with an array of advanced sensors, vision systems, and sophisticated safety features that enable them to interact safely and seamlessly with human workers. This unique characteristic distinguishes cobots and makes them ideally suited for a wide range of applications in manufacturing, including assembly lines.
The Rise of the Cobots
Cobots are engineered to collaborate with their human counterparts, assisting and augmenting their capabilities rather than replacing them. Unlike traditional robots that require skilled programmers to set up and operate, cobots are designed to be user-friendly and easily programmable, often by non-specialists. Unlike traditional industrial robots that are often isolated behind safety barriers, cobots are built with sensors, vision systems, and safety features that enable them to interact safely and seamlessly with human operators. This characteristic sets them apart and makes them ideal for a wide range of applications in manufacturing, including assembly lines. This accessibility and ability to work in close proximity to humans open the door to a host of productivity benefits in the assembly line environment.
Enhanced Productivity
The integration of collaborative robots into assembly lines has brought about several substantial improvements in productivity:
Speed and Precision
Cobots are capable of performing repetitive tasks with remarkable speed and precision. They don’t suffer from fatigue or distractions, and their consistency ensures that tasks are completed accurately and quickly. This has a direct impact on assembly line efficiency, reducing the time required for tasks that might be error-prone when performed by humans.
Increased Throughput
Cobots can work around the clock without breaks, significantly increasing an assembly line’s throughput. They can be programmed to work at a consistent pace, eliminating bottlenecks and ensuring a steady flow of production.
Flexible Automation
One of the most notable advantages of cobots is their flexibility. They can be quickly reprogrammed to perform different tasks, making it easier for manufacturers to adapt to changing production demands. This is particularly beneficial in industries with fluctuating or customized product requirements.
Improved Resource Allocation
By offloading repetitive and physically demanding tasks to cobots, human workers can focus on more complex and value-added activities. This not only improves overall job satisfaction but also allows companies to utilize their workforce more efficiently.
Safety and Collaboration
The term “collaborative robot” underscores a critical aspect of these machines — safety and collaboration with human workers. Cobots are designed with built-in safety features, such as force sensors, vision systems, and the ability to stop or slow down when they encounter an obstacle. This ensures that they can work in close proximity to humans without posing a safety risk.
Reduced Workplace Injuries
With the ability to collaborate directly with humans, cobots contribute to a safer work environment by minimizing the risk of accidents and injuries. They can handle heavy lifting, repetitive tasks, and other physically demanding jobs that may lead to worker strain or injuries.
Ergonomic Benefits
Cobots can be programmed to handle tasks that are ergonomically challenging for humans. This means that repetitive strain injuries and other musculoskeletal problems are less likely to occur on the assembly line.
Improved Quality Control
Cobots can be equipped with vision systems to perform real-time quality control inspections, ensuring that every product meets the required standards. This contributes to higher product quality and reduces the chances of defects reaching the market.
Case Studies in Assembly Line Productivity
To underscore the practical impact of cobots on assembly line productivity, consider these case studies:
- BMW: BMW employs collaborative robots on their assembly lines for tasks such as installing parts and handling heavy materials. This has not only improved production efficiency but has also led to a 50% reduction in errors, ultimately enhancing product quality.
- Flex Ltd.: Flex, a global manufacturing solutions provider, has integrated cobots into their assembly lines for electronic devices. They’ve seen significant increases in productivity and assembly line flexibility, allowing them to quickly respond to changing customer demands.
- Universal Robots: As a leading manufacturer of cobots, Universal Robots has numerous case studies highlighting how their robots have revolutionized assembly line productivity across various industries, from automotive to electronics.
The future of Cobot Manufacturing
While the adoption of collaborative robots in manufacturing is growing, challenges remain. These include the initial cost of implementing cobots, the need for specialized training for operators, and ongoing maintenance. As technology evolves, we can expect further advancements in cobot capabilities, making them even more versatile and user-friendly.
Collaborative robots are transforming assembly line productivity by offering speed, precision, flexibility, and enhanced safety. Their ability to collaborate seamlessly with human workers makes them invaluable tools in modern manufacturing. As industries continue to embrace this innovative technology, we can anticipate an era where assembly lines are not only more efficient but also safer and more adaptable to changing market demands. The impact of cobots on assembly line productivity is nothing short of revolutionary, and it promises to reshape the future of manufacturing.